One of my most desired features of our new home was to have reclaimed lumber floors. About 4-5 years ago, Colton and I went to our local home show and we met a father / son, owners of Tuscarora Wood, who took down old barns and milled the wood into flooring. I kept them in mind and Preston & I saw them again this winter at the show. They have gotten so busy, they no longer take down the barns and just buy from those who do. They sell mostly wholesale to companies out west. Compared to buying hardwood floors from a local flooring store, I thought their prices were very reasonable and not much more. There just isn't anything that compares to the richness and natural beauty.
If you remember, we also pulled out some of the old oak floors from our old house. They were a full 1" thick, but the tongue and grooves were in rough shape, so they were able to take the wood to their mill and mill all four sides with new T&G. This was white oak and some ash, so we put that in the entry. The rest we purchased from them was red oak which is in the living room and kitchen.
When they provided the quote for about 1100 square feet, they broke out the line item for material, installation, sanding & finishing. Since we had sanded and finished the floors in our old house, this seemed like something we could do ourselves and save the $4100.
To save another $300 in pre-delivery charge (net $200 after fuel), Preston drove up to Covington about an hour away and picked up the pallet of wood. We offered to bring the wood into the house ... 3 or 4 boards at a time and have it stacked for them. 2-1/2 hours later we had it all in there. When I save money by doing something myself, I like to calculate the "hourly rate" for the labor. Not counting the drive time, just stacking the wood came out to $40/hour. Not too bad.
After they installed the floors, Rod mentioned that they would plug all the round holes (where pegs used to be when they were beams) with slices of old pegs and epoxy them in. He also offered to epoxy the other "imperfections" ... I thought that would be a good use of money vs. time, so we had him do that. What I underestimated was how "generous" they would be with the epoxy. All of the epoxy would then need to be sanded down smooth with the surface of the floor. If you've never sanded epoxy, let me tell you that a walk-behind drum sander with 60-grit paper will just ride over the surface of an epoxy "lump."
So we rented the drum sander, a disk sander (also a walk-behind) and an edge sander ... which is a single disk sander, but must be handled on your knees (or bent over). We started sanding Thursday night ... 4 hours later (8 between the 2 of us), it still looked like an epoxy war zone. We hit the high spots, but there was still so much to be done.
I took Friday off and started at 8am. After a few minutes with a little hand sander, I thought the only thing that was going to get this was the edge sander. This thing is super heavy and if you don't have a tight grip on it, it will take you for a ride. But it was the only thing that would cut thru the epoxy in any reasonable amount of time. So I spent the entire day wrestling with this monster across 1100 sq feet.
Preston came home mid-day and helped a bit more in the afternoon. By 8pm, I could barely move and we still weren't done... close, but not quite. So we went to bed and got up early to sand a couple more hours. We loaded the sanders up and returned them to the rental company. I came home and had just a little touch up to do with our sander. Then it was time to vacuum and clean the floors. That took another 5 hours or so. It's one of those really important steps that you don't want to rush thru. I started by sweeping the dust off the walls, then vacuuming with the grain and then against it. Then mop the floor with paint thinner to get up the last little bit.
Finally about 5pm on Saturday, I was ready to start the finish. We used Waterlox which is a tung oil-based resin. I love this stuff. It soaks into the floors, but provides a waterproof surface at the same time. Unlike polyeurethane, it doesn't just sit on top like a candy coating. And if you have a spot that gets damaged, you can just sand it and brush on more in that one spot. Plus it just looks rich and "old."
Since we bought it in 2005 for the old house, the price at gone from about $55 / gallon to double that. I learned later that the Ohio EPA had passed VOC regulations and required the product to meet low VOC standards to be sold in the state. So, that doubled the estimate on the floor finishing!
I put a coat on Saturday, another Sunday around noon and got up at 4am on Monday and put on another coat before going to work. It then needed to sit for 48 hours before we could cover with rosin paper for foot traffic.
So let's see if our 60 hours of labor was worth it ...
Sander rental .... $280
Waterlox .... $860
Finishing supplies ... $40
Breakeven labor costs $50/hour ... not too bad!
But it still confirms why I went to college ... back to work Monday to REST!
So here are pictures ...
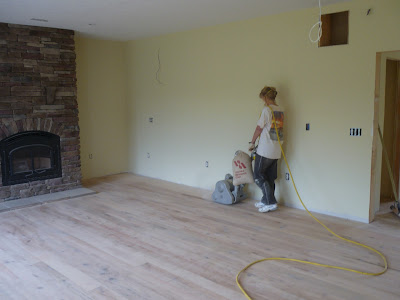 |
sanding with the drum sander |
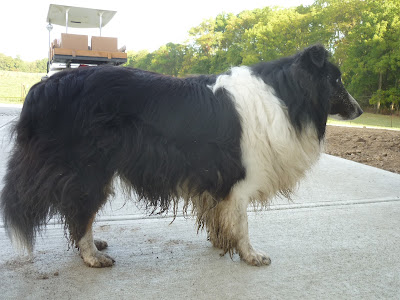 |
so imagine you've been sanding for hours and your dog comes into the house on the bare wood floors looking like this ... |
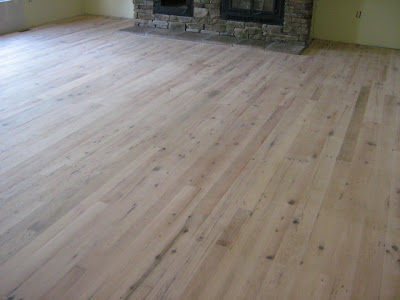 |
finished sanding |
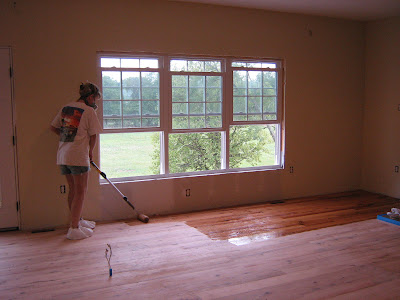 |
start the finishing ... pretty easy ... just roll it on |
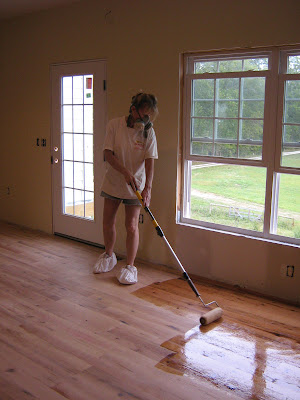 |
even low VOC requires a mask |
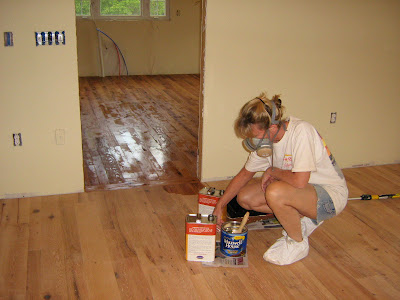 |
first coat looks pretty blotchy |
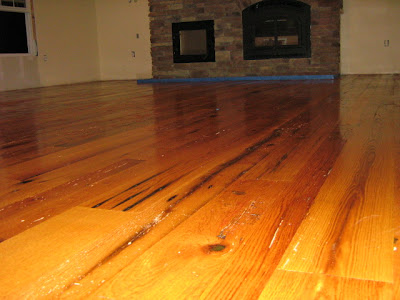 |
2 coats done |
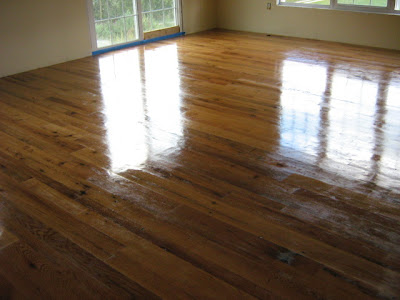 |
a little glossy but that will tone down in the first couple months as it cures |
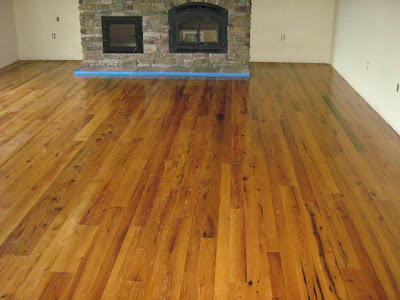 |
3 coats done |
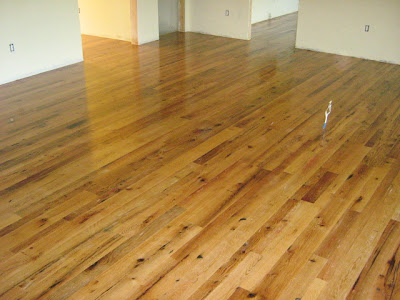 |
that wire sticking up will be an electrical outlet. |
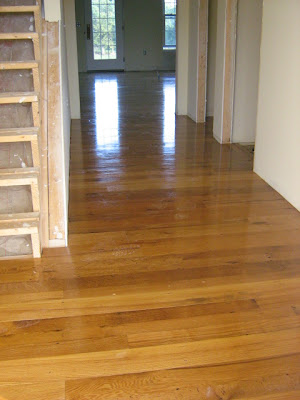 |
this is the entry ... white oak from our old house. |
After the 2 days of drying, there were 2 moths that had landed on the Waterlox when it was wet. What a mess the dust on those little creatures can make! Their wing dust dried into the varnish, so I had to sand it down a bit to get it out. Will finish with a final coat when the house is complete / before moving in.